The Four Phases of Onsite Process Validation for Pet Food
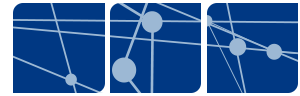
By Martha Kimber and Shirin Abd
Between 2003 and 2022, over 23% of all pet food recalls in the United States were attributed to Salmonella contamination. Alarmingly, 94% of these recalls were classified as Class I, posing serious health risks to pets and their owners (DeBeer et al., 2024)1. The continued detection of pathogens in dry pet foods underscores the industry’s need for a broader understanding of the lethality of various preservation methods and technologies used during manufacturing.
Processes such as drying, extruding, and baking, are often claimed to serve as effective “kill-steps” against microbial pathogens; however, scientific data demonstrating the efficacy of these processes is sometimes lacking. Here, we have highlighted best practices that pet food processors may use to scientifically demonstrate that a given process, or “kill step,” can deliver the required microbial reductions to ensure the safety of their product.
Phases of a Successful Onsite Process Validation
One widely used approach to ensure your process can achieve the necessary microbial reductions is to perform an onsite process validation at the manufacturing facility using a non-pathogenic surrogate organism. These validation studies typically consist of four key phases:
Phase 1: Identify Critical Factors
The first step is to identify the critical factors for the product and process which may impact microbial survival. These could include product factors such as water activity, fat, moisture, pH, formulation, piece size, etc.; while the process factors may include process temperature, process duration, batch size, and many other variables related to the specific type of processing used. Representative conditions are then selected to serve as the baseline for subsequent validation phases.
Phase 2: Select an Appropriate Surrogate
The surrogate organism selected for the validation study should be based on characteristics such as non-pathogenicity, stability, ease of cultivation, and correlation to the target pathogen(s) (which often includes but is not limited to Salmonella). This ensures that the surrogate’s behavior in the actual product and under the selected processing conditions accurately reflects that of the target pathogen(s). Data from scientific literature for similar products and processes and/or laboratory correlation studies may be helpful in making this determination.
Phase 3: Execute the In-process Validation Study
With the plan defined, the validation study is then executed using the unit operation at the at the manufacturing facility. Key activities include:
- Preparing inoculated product with the selected surrogate.
- Processing the product according to the conditions selected in Phase 1.
- Collecting test parameter data.
- Enumerating the surviving surrogate organism in post-process samples.
Phase 4: Prepare a Comprehensive Report
The final step is to document and report the results of the study. The report should include:
- A description of the product and process parameters used for the onsite validation.
- A detailed study protocol.
- Study results for all samples tested.
- A conclusion that summarizes the efficacy of the process to deliver a log reduction of the surrogate and how the observed reduction correlates to the log reduction of the target pathogen.
Applications in Pet Food Manufacturing
Process validations may of course vary across pet food processing operations and applications. Some examples of where validation may apply include, but are not limited to:
- Baking processes for pet treats.
- Extrusion processes for kibble.
- Drying processes used in multi-component pet food treats.
- High pressure processing (HPP) for raw meat pet food prior to freeze-drying.
Each of these processes presents unique challenges and opportunities for microbial growth, which will define the critical factors necessary in the process validation study. In some cases, a laboratory benchtop study will suffice, while in other cases an onsite validation is more appropriate.
Getting Started with a Process Validation
As the pet food industry continues to strive for higher levels of safety and quality, process validations are critical to ensure that these goals are met. Whether you are refining an existing process or introducing an entirely new product line, an expert consultation from our Advanced Food Microbiology team is where to start. We have extensive experience in process validations and a steadfast commitment to supporting manufacturers in achieving their food safety goals.
Contact us today to learn how we can assist with your pet food process assessment.
Additional Resources
Exploring Microbiological Control: Testing Methods for Preservative and Antimicrobial Effectiveness
Resources
- DeBeer, J., Finke, M., Maxfield, A., Osgood, A. M., Baumgartel, D. M., & Blickem, E. R. (2024). A Review of Pet Food Recalls from 2003 through 2022. Journal of Food Protection, 100199.