Pilot Scale and Small Batch Production: Ensuring Success in Product Development
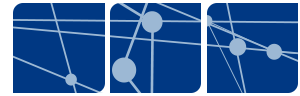
For companies developing food, beverage, dietary supplement, and pet food products, moving from concept to commercialization requires more than just a great idea. Pilot-scale production serves as a bridge between R&D and full-scale manufacturing, offering critical insights into ingredient interactions, processing challenges, and packaging performance.
Whether you’re showcasing products at industry events, launching test markets, or refining formulations, pilot production must be executed with precision. Overlooking key factors can lead to unexpected stability issues, regulatory non-compliance, or costly reformulations down the line. This paper highlights the essential elements of a successful pilot-scale production strategy.
Key Considerations for Pilot-Scale and Small-Batch Production
- Food Safety & Regulatory Compliance
- Is the product being distributed beyond internal testing? If so, are the proper food safety protocols in place?
- Have you accounted for Good Manufacturing Practices (GMPs) and ensured the necessary manufacturing certifications and process documentation are secured?
- Understanding the intended use and distribution of the product ensures compliance while minimizing safety risks.
- Quality Control & Consistency
- Have you defined the key quality parameters for your product?
- How will you measure active ingredient levels, sensory attributes, and stability?
- Small formulation adjustments can cause significant shifts in flavor, texture, or functional performance. A well-structured quality control process ensures consistency between pilot runs and full-scale production.
- Troubleshooting Production & Process Variables
- What happens if the process doesn’t go as planned?
- Have you tested how ingredient interactions will behave under real-world processing conditions?
- Common challenges include:
- Protein instability – Foaming or precipitation during filling.
- Ingredient separation – Unexpected changes in solubility or phase separation.
- Texture inconsistencies – Variability in emulsification, aeration, or gelling.
- Understanding processing levers and formulation adjustments ensures a smoother transition to large-scale manufacturing.
- Packaging Performance & Stability
- Does your packaging choice align with your product’s formulation and shelf-life needs?
- Have you tested for potential interactions, such as:
- Corrosive ingredients in metal cans (e.g., energy drinks reacting with aluminum).
- Moisture-sensitive formulations in pouches leading to clumping or degradation.
- Heat exposure during hot-fill processes impacting product stability.
- Pilot runs offer a crucial opportunity to validate packaging performance before scaling up.
Conclusion & Next Steps
Pilot-scale production is a pivotal step in transforming product concepts into market-ready solutions. By addressing food safety, quality control, processing challenges, and packaging stability, companies can avoid costly mistakes and accelerate commercialization.
Ready to optimize your pilot production? Contact us to discuss how we can support your next product launch.
Meet the Author
Ed Collins
Director of Product Development
The National Food Laboratory
Ed Collins is the Director of Product Development for The National Food Lab, a division of Eurofins and has a BS in Agricultural Engineering and an MS in Food Science. During his 35-year career in the beverage and food industry, he has worked on just about every form of beverage, nutritional product, meal, or snack for clients at all stages of the development cycle. With a strong focus on collaboration and technical excellence, he works closely with our clients to bring their product concepts to life.
At The National Food Lab, we specialize in guiding brands through every phase of product development—from benchtop formulation to pilot production and full-scale commercialization. Our expertise ensures your pilot runs provide actionable insights, reduce risk, and set your product up for success.