How to Have Confidence in your Finished Product and Where to Turn When Something Goes Wrong
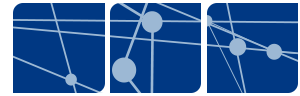
Your goal is to manufacture a safe product that meets the claims on your label.
How are you ensuring that your finished product will do this?
Proactively, or retroactively?
Putting a proactive plan in place to assess ingredient safety and quality is key to producing finished products that meet all of your quality standards. Having a partnership with an accredited, independent (third-party) laboratory just in case something goes wrong is a must.
Why Assess Ingredient Safety?
Assessing each ingredient, as it comes in, is not only the right thing to do to ensure the safety of your finished product, but it is also a requirement under the Food Safety Modernization Act (FSMA). Creating a testing plan is critical to bolstering product and brand stewardship and your company’s reputation.
A proactive plan will increase:
- Product quality, and safety
- Product performance
- Control over your supply chain
- Confirm product label claims
- Enable increased market share
- Mitigate risk in the event of off spec (“non-conforming”) ingredient arrival at your facility
- Improve your company’s bottom line
In addition to these things, a proactive testing plan will help prevent recalls and detect adulteration or food fraud early on. This will greatly reduce the legal and insurance claims downstream. Not to mention that it will give you and your customer’s confidence around what is listed on your product’s label which strengthens your brand and industry reputation.