Good Laboratory Practices vs. Good Manufacturing Practices: What's the Difference?
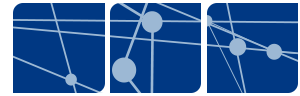
Although the terms “Good Laboratory Practices” (GLPs) and “Good Manufacturing Practices” (GMPs) are similar, these approaches have very different purposes. While GLPs are used in the context of research and development, GMPs apply when products being manufactured for sale. Both can apply to product testing, but during different phases of the product development process. It is helpful for many companies manufacturing and selling ingredients, animal health and feed additives, OTC products, and dietary supplements to fundamentally understand the differences between GLPs and GMPs to ensure proper use during R&D and manufacturing.
Good Laboratory Practices
Good Laboratory Practices (GLPs) are quality management programs that were first adopted in 1972 in Denmark and New Zealand. The US FDA released its own GLP regulations in 1978-79. The goal of these regulations is to ensure testing in a preclinical or product development context is done using reliable methods and excellent recordkeeping so that companies can provide regulatory bodies with accurate and auditable data.
In general, GLPs apply to premarket or preclinical research and testing in regulated industries including pharmaceuticals, animal health products and medicated feed, food additives, medical devices, and food packaging.
GLPs include numerous measures to promote the reliability of data. For example, each study must have a study protocol that is approved by the testing facility’s management. Procedures and calibrations must be recorded, dated, and signed. Records must be retained securely for two years after completing the study or, if the studies are used to apply for a marketing permit, for at least five years after the registration date.
Good Manufacturing Practices
Good Manufacturing Practices ensure that manufactured products meet quality standards by setting specifications and requirements for the process by which they are produced and tested. In the US, GMPs are Food and Drug Administration (FDA) regulations that apply to the manufacture of pharmaceuticals, medical devices, some foods, dietary supplements, and a few other products.
GMP regulations are far-ranging and apply to not only testing but every step of the manufacturing process. The focus is on promoting consumer safety by preventing things like cross-contamination, microbial contamination, or lack of drug efficacy due to problems in the manufacturing process.
In the US, “current GMP” (cGMP) is a synonym for GMP, as cGMPs specify the FDA’s minimum requirements for manufacturers. The FDA adopted the term “current GMP” to emphasize that manufacturers need to continually re-evaluate their manufacturing practices to stay up-to-date as technology changes in their industry.
GMPs include strict controls on the following, known as the Five Ps of GMP:
People involved in manufacturing must be trained in cGMPs and in their roles and responsibilities in maintaining quality.
Products must be produced according to the standard operating procedures (SOPs) and must be appropriately tested before release to consumers.
Processes should be well-designed, well-documented, and understood by all employees
Procedures must be standardized and maintained throughout the manufacturing process.
Premises should be designed in ways that reduce the risks of contamination and accidental mislabeling; there are requirements for washing facilities, sewage, lighting, and plumbing. Testing equipment accuracy, sensitivity, specificity, and reproducibility must be documented and must meet specifications.
When to Use GMPs vs. GLPs
The purpose of GLPs is to ensure pre-market data integrity, so use them for testing that occurs during product development. GLPs' roots are in the pharmaceutical industry, where the approach is used during preclinical drug development and to generate data for FDA submission to obtain drug approval. However, GLPs also apply to food and color additives, food packaging, food contamination limits, and medical devices, since developers of these products need to submit data to gain regulatory approval as well.
By contrast, GMP regulations apply when products are being manufactured to be sold to consumers, so use it for lot or batch testing, testing of ingredients from suppliers, and any other testing that occurs in the course of manufacturing.
In the most basic sense, GLPs focus on product development, and GMPs focus on production.
For example, if a company was developing a medicated animal feed, GLPs would apply when generating data for registration or approval, including animal safety and over dosage studies in the target species. Once the product is finalized, GMPs would apply during routine manufacturing and to any testing of ingredients as well as testing of the completed product before sale to consumers.
As another example, a company developing a new food additive would need to generate data on the safety of the additive, and this testing would be performed under GLPs. If the FDA accepts the product for use in food, its manufacture and associated food safety testing would then be performed under GMPs.
GLPs vs. GMPs: Know the Difference
Understanding the differences between GLPs and GMPs and their purposes and applications is essential. The network of Eurofins laboratories has experience with both approaches, and we offer GLP-adherent testing as well as support in implementing GMPs in your facility. Wherever you are in your product development or manufacturing process, our experts can help you find the right testing solutions.