Expanded Capabilities to Support Validation of Disposables for Bioprocessing
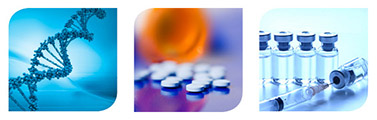
by Jon Kauffman, Ph.D., Biopharmaceutical Director
A current trend in biopharmaceutical processing is the utilization of single use products. These disposable products can eliminate costly capital expenditures for stainless steel tanks and piping and reduce the risk of cross-contamination between production batches. However, the materials used to construct these components may introduce unwanted contaminants into biopharmaceutical intermediates and final products. Many of these contaminants are added to single-use products to enhance usability of the material. Sources of these contaminants include antioxidants, anti-static agents, stabilizers, colorants, plasticizers and lubricants. In addition to the additives, contaminants from the polymerization process, such as monomers, oligomers and polymeric fragments are possible. Therefore, careful evaluation of single-use systems is required.
Evaluation of these impurities and the validation of disposable systems can be an arduous task. Potential contaminants must be identified and quantified using a wide array of microbiological and analytical approaches. Data generated from these studies must undergo toxicological assessment so that risk-based, informed decisions can be made on the acceptability of single-use products and disposables. Validation should be addressed early in the process to avoid regulatory delays for the drug manufacturer.
These disposable systems contain a wide range of fluids including culture media, additives, buffers, bulk intermediates and final formulations. In many cases microbial control or sterility is required to ensure product purity and safety. Radiation sterilization is a common means of microbial control in single-use systems. As part of the validation of sterilization processes or as part of the materials qualification program, sterility and /or endotoxin testing is required.
Single-use systems pose unique challenges during testing due to their size and complexity. A large scale system, could be, for example, a 3000 L bag connected to several meters of tubing, high area filter housing that could be 10 inches or larger, and a connector with a complex design. Large articles are especially difficult to manipulate aseptically. Specific issues include introducing such large articles into controlled spaces, aseptically adding or removing fluids to the test article, and aseptically handling large fluid volumes required for testing. Cleanrooms have the advantage of offering considerable space for operators and materials, compared with isolator technology and provide a solution for sterility testing of large single-use systems.
Non-microbiological contaminants fall under the label of extractable and leachable compounds. Extractables are compounds that can be extracted from a component under exaggerated conditions such as in the presence of harsh solvents and/or at elevated temperatures. These compounds have the potential to contaminate the drug product. Leachables are compounds that leach into the drug product formulation from the component as a result of direct contact with the formulation under normal conditions. Leachables are typically a subset of extractables. Nitrosamines and polynuclear hydrocarbons (PAHs), which are classes of carcinogenic compounds found in rubber, are examples of potential leachables.
Many drug products are distributed or administered in packages made of plastic and rubber components, and therefore, phthalates, PAHs, and/or nitrosamines could potentially come into contact with the drug product and be passed on to the patient.
Design of these studies is critical. Extraction of the components of interest should represent worst case conditions, but not stress components to the point of material breakdown. When determining extraction conditions, the shelf life of the product must be considered for packaging, and the contact time and temperature must be considered for manufacturing materials. Based on this information extraction conditions are selected that will result in extract solutions that will be tested for extractable compounds. These extracts must be screened for a wide array of potential contaminants using analytical approaches such as GC/ MS, LC/MS, and ICP/OES.
The results of the extractables testing should then be subject to a toxicological evaluation to determine the potential risk to product from the observed compounds. The toxicologist will need to take into account the dose delivered to the patient, the frequency of dosing as well as the result from the extractable study. This information will be utilized to determine a tolerable intake and tolerable exposure (TE) for each compound, and the TE value will be compared to the amount of compound released in the extractable study.
The presence of compounds determined to be at risk in the final product need to be monitored. Methods specific for these compounds need to be developed and validated in the product matrix to allow for monitoring for the presence of the compound. These methods are commonly utilized as part of a stability study to prove that the leachable compound of interest does not adulterate the product during the determined shelf life of the product.
Eurofins Lancaster Laboratories provides these complete services in both the US and Europe, coordinated by expert project managers. For more information, contact your Project Manager or Business Development